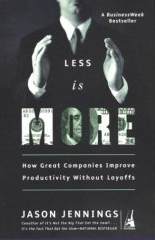
Veamos lo que dice Jason jennings en su libro menos es mas:
¿Qué es Kaizen?
El vocablo kaizen, traducido del japonés como “mejoramiento continuo”, apareció por primera vez en Estados Unidos en los años 70, cuando la industria americana comenzó a sentir colectivamente las bofetadas del Japón, sin nunca darse cuenta de que los iniciadores del concepto había sido sus propios filósofos estadounidenses.
Hace más de 100 años, Henry Ford desarrolló activamente uno de los primeros sistemas de producción en serie del mundo, con el fin de mejorar la productividad. Impulsado por una meta intuitiva de bajar el precio de un automóvil al nivel en el cual la persona que lo construía pudiera comprarlo, Ford trabajó simultáneamente en muchas técnicas diferentes, entre ellas la de los componentes intercambiables, la de las líneas de producción y la de los procesos estandarizados. Concentró su pensamiento en el perfeccionamiento de la producción en serie, proceso que en últimas permitió reducir el precio de un automóvil de 700 dólares a menos de 300.
A finales de los años 20, un empresario japonés llamado Taiichi Ohno visitó a Henry Ford para conocer la manera como las compañías estadounidenses utilizaban la producción en serie. El hallazgo más importante de Ohno fue que Ford había logrado reducir el tiempo necesario para fabricar un automóvil de 700, minutos a menos de 90.
Durante su viaje, Ohno también visitó los supermercados americanos, desconocidos por ese entonces en el Japón. Quedó profundamente impresionado con la manera como se apilaban los alimentos en las góndolas y se reemplazaban a medida que iba necesitando. Esta observación le dio una idea fascinante que contribuiría al desarrollo de la producción japonesa. A diferencia de la situación en los Estados Unidos, donde Ford tenía acceso a capital abundante para comprar materiales antes de tiempo, y mucho espacio para amontonar inventarios enormes, en Japón había escasez de espacio y de materiales. Ohno reconoció que podría ahorrar sumas cuantiosas al no almacenar inventarios enormes de componentes.
Apenas un par de años después, la gente de Toyota, compañía que venía de la industria de los telares y los textiles, comenzó a fabricar automóviles para el gobierno japonés y utilizó para ello las técnicas que Ohno había observado durante su visita a los Estados Unidos. Ohno juntó las ideas de Ford, el concepto del inventario justo a tiempo tomado de los supermercados, y los escritos de Frederick Taylor, otro estadounidense. Todo marchaba bien para Ohno y Toyota cuando se produjo el cataclismo de la Segunda Guerra Mundial y todas las compañías japonesas entraron en quiebra o se vieron al borde de la misma. Toyota, desesperada por sobrevivir, comenzó a importar las ideas de otro consultor americano, W Edwards Deming, cuyas recomendaciones sobre el control de calidad y la calidad estadística habían sido rechazadas alegremente por la industria estadounidense.
Finalmente, hacia finales de los años 60, Toyota reunió todas las piezas y así nació formalmente la idea del kaizen. La compañía ofreció empleo de por vida con la condición de que los empleados utilizaran las técnicas innovadoras encaminadas a facilitar, acelerar y mejorar su trabajo y a orientarlo hacia la calidad. La gerencia insistió en el compromiso de todos con la eliminación del desperdicio. Los resultados fueron poco menos que espectaculares y las compañías japonesas que acogieron el kaizen alcanzaron una tras otra unos niveles de productividad muy superiores a los de sus competidores de los Estados Unidos.
La ironía más grande es que, en 1979, Ford lnc., la cuna de todo el asunto, decidió adquirir una parte de Mazda a fin de aprender a aplicar los principios del kaizen.
No hay comentarios:
Publicar un comentario